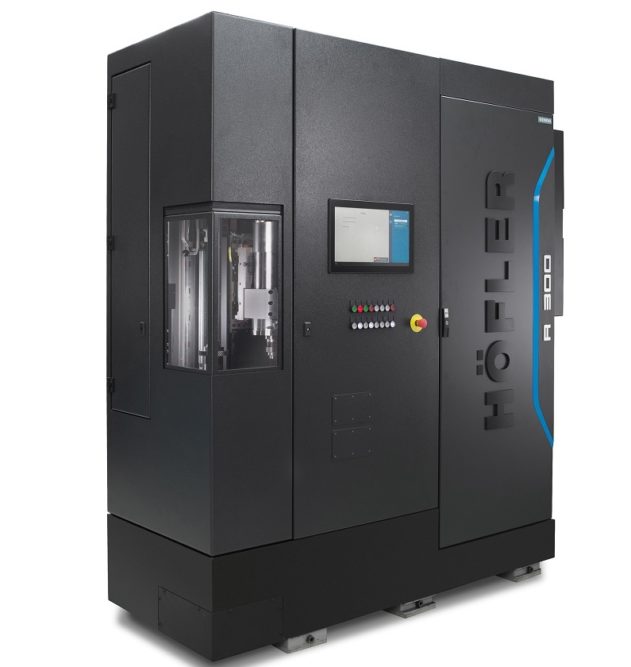
The Höfler Cylindrical Gear Roll Testing Machine R 300.
Klingelnberg Offers Gear Production Technology at IMTS 2022
Klingelnberg will be featuring the latest gear production, calculation and measuring technologies during IMTS in Booth #236935. Here are a few highlights:
R 300 – The Gear Noise Finder
The Höfler Cylindrical Gear Roll Testing Machine R 300 is the latest machine development in the area of cylindrical gear technology. Due to the increasing quality requirements in large-scale transmission manufacturing, some transmission and vehicle manufacturers now require a certificate of quality for all gears installed in the powertrain. A further driver of ever-higher inspection levels is e-mobility, which places much higher demands on the noise behavior of a transmission due to the elimination of the combustion engine. To meet this challenge, Klingelnberg is building on roll testing technology, a familiar method from the bevel gear industry that is now moving into the world of cylindrical gears. Designed for all five roll testing methods, this compact machine is the ideal solution for anyone who wants to combine inspection cycles and reduce disassembly costs while benefiting from a user-friendly design. The many quality control requirements for gears can only be met with a flexible test machine.
Depending on the configuration, the R 300 provides the option of using all five roll testing methods. These include the single flank test, structure-borne noise and angular acceleration test, double-flank and helix roll test. Thus, the R 300 can be used at every point in the production process chain for cylindrical gears – from monitoring the soft cutting to checking the hardening distortions, to evaluating the noise behavior of the installation-ready gear.
In terms of axis traversing paths, the R 300 covers the same component spectrum as the tried-and-tested Höfler Generating Gear Grinding Machine Speed Viper. Wheel components can be tested up to an outside diameter of 300 mm. In conjunction with the optional counter support, shafts up to 800 mm long in extreme cases can be analyzed to determine their running performance and noise behavior. Yet the machine’s footprint is a compact 2 m2 – saving costs on expensive production floorspace.
Reducing Measurement Times in Serial Measurement with a Hybrid Solution
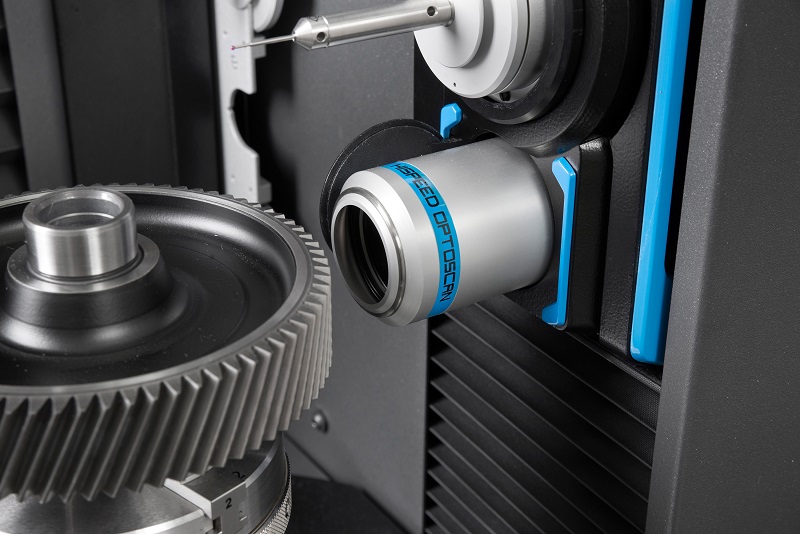
The HISPEED OPTOSCAN offers precise measurements from Klingelnberg.
Klingelnberg Hybrid Metrology is a smart combination of tactile and optical measuring technology. An optical sensor system developed specifically for gear measurement, as well as the rapid changeover between the 3D NANOSCAN tactile sensing system and the HISPEED OPTOSCAN optical sensor, enable flexible, fast, and highly precise measured value acquisition under all conditions.
With the current version of this option, pitch, tooth thickness, and gear concentricity can be measured optically on cylindrical gears, making it possible to increase the number of measurements for shop-floor quality control per shift and machine by 20 % on average. The appeal of this option grows with the number of teeth on the gear to be inspected. Approximately two minutes of quality control time can be saved per gear when it comes to gears of interest to the automotive industry. For gears used in electromobility, which frequently have a large number of teeth, this measuring time savings is even greater. And optical pitch measurement, like tactile pitch measurement, is performed in accordance with VDI/VDE 2613 Group I.
The measurement and analysis are performed using Klingelnberg’s well-known cylindrical gear software. With the latest version of the software, hybrid use of tactile and optical precision measuring centers as part of a networked system is made easy. Because the optical measuring system used by Klingelnberg is highly accurate on nearly every metallic surface, approximately 90 % of cylindrical gears in a typical portfolio are suitable for optical measurement. All Klingelnberg precision measuring centers in the P 26 to P 100 series can be optionally equipped or retrofitted with an optical solution.